Hello, welcome to Wuhan Xiao Rui Machinery Co. Ltd. website!

Discussion on the Influence of Design Defect on Production
- Categories:Industry news
- Author:
- Origin:
- Time of issue:2016-10-22 14:19
- Views:
(Summary description)Abstract: To construct a modern new wall material enterprise, the project design must be designed on the basis of scientific argumentation, combined with the actual situation of the country and the la
Discussion on the Influence of Design Defect on Production
(Summary description)Abstract: To construct a modern new wall material enterprise, the project design must be designed on the basis of scientific argumentation, combined with the actual situation of the country and the la
- Categories:Industry news
- Author:
- Origin:
- Time of issue:2016-10-22 14:19
- Views:
Abstract: To construct a modern new wall material enterprise, the project design must be designed on the basis of scientific argumentation, combined with the actual situation of the country and the laws and regulations of the country, and integrated many factors. Once the design flaws, it will give the future production of a great deal of trouble, resulting in serious losses.
1 Introduction
Construction of a modern new wall materials enterprises, the general investment in tens of millions of dollars. Before the construction of scientific proof, multi-inspection is essential, a little careless, will be less credibility of the designers, builders, equipment manufacturers to the 忽悠。 They only for their own little petty profits, not for the smooth production of the builder to consider (but does not rule out the ill-considered factors such as designers). Design defects, it will give the future production of a lot of trouble . Such as the construction of a southern enterprise a high degree of automation of a code burning process (with a 7.3m large-section tunnel kiln), but found in the design of the existence of multiple defects, to the actual production has brought serious consequences. Is the design of this production line defects in the analysis, with the industry colleagues to explore, in order to be able to give some owners warning.
2 crushing process is not suitable for high moisture content of raw materials
The rainwater in the south more, sometimes in January under the rain more than 20, the moisture content of raw materials are generally more than 12%. This is well known, but the production line design of the raw material crushing process is: jaw crusher - double rotor broken Machine - hammer crusher - drum sieve - biaxial mixer - aging library. Design production per hour to prepare mixture 60t, while the actual output less than 20t per hour.Every day the equipment running 20h, also difficult to meet the molding needs. It can be said that the mixture in the aging of the library was too late to be transported to the aging of the molding section. Why does this happen? The main reason is that the crushing process does not meet the high water content of raw materials. Due to the high water content of raw materials, crusher often blocked. Clean up a jammed crusher will need more than 6h, sometimes blocking several times a day. Clean up finished broken, broken and blocked, clean-up after the break, the drum sieve and plugged into the material does not leak the “barrel.” Gaode the workers physically and mentally tired, complaining. To this end had to adjust the feed volume, by extending the crusher working time to break the raw materials, high power consumption, serious wear and tear equipment, current overload tripping occurs. Sometimes 1h can only output more than ten tons of the mixture. One side is the raw material preparation workers busy cleaning crusher, the other side is the blank workers anxious and other materials, engage in the whole plant leading workers all the focus, depression. In order to protect the production, only the coarse broken and broken broken grate plate off a few, the screen of the drum screen from 2.5mm to 3.0mm. But to produce the mixture particle size distribution is unreasonable, 0.05 Mm below the fine powder accounts for only about 2, to the subsequent molding great difficulties, the quality of brick can be imagined. As the raw material crushing process, seriously hampered the normal production of the enterprise, such as the market needs of the high porosity hollow brick simply can not produce, is the production of ordinary solid brick-based. Tens of millions of investment, can only produce ordinary solid brick, I do not know benefits come from.
3 molding defects
First, the code blank machine installation position is poor, the code brick side of the side wall is only 200mm away from the two workshops have 60m ventilation window, the temperature sometimes as high as 40t or more, in addition to brick temperature is high, it can be said just production Out of the brick in the air is not the flow of high humidity environment, brick is easy to soften, kiln car running a little collapse occurred. So that had to stop production, organization staff to clean up, to the high temperature production has brought great trouble, that affect the production and affect quality.
Second, the host of the upper and lower machines are not designed inverter. As a host to produce a variety of product specifications, require the host speed is different, so as to ensure the smooth extrusion of different specifications of the product. But the extruder on the production line is a speed, obviously unreasonable.
Third, mechanical arm exhibition is not enough. The designer only consider the code ordinary solid brick, but the code 190mm hollow brick, the top layer of brick buried, because the robot arm lift height is not enough, the plywood open up height can not reach the height of brick, had to splint 50mm, Small brick area, a strong pressure on the brick unit, and often the brick clip deformation or invisible internal injuries, affecting product quality.
4 defects in the furnace
First, the kiln specifications have limitations. The face of fierce market competition, a line to produce a variety of product specifications to meet market demand. Therefore, in the construction of drying room and baking kiln to take into account the production requirements of a variety of product specifications, not only the production of ordinary solid brick specifications to build. Such as the production of hollow bricks, blocks and other modules of the brick, the kiln as the width of the limit, resulting in the top gap is too large, affecting the drying, roasting effect (author of “brick” magazine 2015 2 “ Clay fly ash sintering brick making, ”the article talked about this phenomenon.) The plant kiln car away from the kiln top is 1730mm, is the code 14-layer ordinary solid brick design, but the production of 240mmX190mm cross-section of the puzzle (193X9 = 1737mm, must consider the shrinkage of the blank, the same below), the drying chamber height is not high enough (1730-1737 = -7mm), code 8 high (193x8 = 1544mm), The top gap of up to 186mm (1730-1544 = 186. This high headspace, the drying effect is naturally not good, roasting energy consumption will be high, but also to the normal roasting brings great difficulty. When considering the production of a variety of products, the height of the tunnel kiln in accordance with the code height of 13 layers of ordinary solid brick, the 1620mm (117X13 +99 mm head gap) high kiln, such as the production of 190mm high and 240mm high block, Is 76mm (l620-154 = 76) and 120mm (l620-250X6 = 120), in addition to the last 120mm of the headspace slightly larger, are able to control the range. Therefore, the design as far as possible to take into account the production of a variety of product specifications.
Second, the code blank is too high. As a result of a code burning process, the raw material plasticity index is only about 7.3, the design is semi-rigid plastic extruder, code blank is too high, easy to lower the body of fracturing or pressure deformation, a little careless will cause Blanking, loss of large, low yield.
Third, the kiln wall, kiln roof insulation performance is poor. Kiln wall outside the maximum temperature of 94 ℃, the roof temperature of the roof up to 110 ℃。 This situation greatly exceeds the national standard “sintering brick factory energy-saving design specifications” and “sintering brick factory engineering design specifications” requirements, do not meet the national norms of shoddy kiln. In the positive pressure from the coal hole to add a little coal, flue gas quickly emerge from the roof. At night from the kiln under the roof can be seen from around the tube plus the fire, showing poor sealing performance. Construction unit requirements kiln unit repair, construction of the kiln, said the drawings by construction Yes, is the design problem. After viewing the drawings and found that the kiln top insulation in this description is very vague, there is no specific construction requirements, it became a “kick the ball” case.
Fourth, the kiln wide and unreasonable design. 7.3m wide kiln car, the design is a row of 1.0mX1.0m ordinary solid brick 6 stack, stacking gap plus up to 1300mm (7300-6OOO = l300mm), coupled with the top gap 106mm, which accounted for three gaps Kiln cross-sectional area of ??22.8%, while the brick gap accounted for only 16.7% of the kiln cross-sectional area; three-gap ventilation area is greater than 6.1% of the brick gap ventilation area, this ratio is clearly unreasonable, the result is often the middle bricks bricks Black heart and charred phenomenon, and the faster the fire line, the more serious charring phenomenon. In addition, the excess air coefficient is not only increase the burden of desulphurization equipment, but also to bring more trouble to standard exhaust.
5 defects in the kiln car
On the kiln car design is unreasonable, a design unit design 7.36mX5.44mX0.84m kiln car, kiln car mat brick is not designed on the expansion joints, between the pad and the brick mat tightly against Together with fixed in the frame brick (with the brick surface flat) in the baking kiln run a few laps, kiln car frame brick was refractory mat brick up or broken. We know that kiln car mat in the baking kiln will reach more than 1000 ℃, due to the role of expansion and contraction, the gap between the pad brick is inevitable, combined with vibration and wind in the kiln running the role of dust, broken bricks Will fall in the pad of the cracks in the brick, with the continuous expansion and contraction. Pad between the cracks in the folder will be more and more things, only cleaning is difficult to clean up, so the brick to move out of the box, brick and brick kiln car was fixed dead, when the pad brick Outside the top of the force is greater than the frame brick and corner brick support force, the box will be the top brick distortion, the top bad and top off. Running more than a year of kiln car potholes, box brick edge is in and out, high and low, and some have a few pieces of brick are top of the top out, and serious air leakage, roasting difficulties, red brick (less fire brick) , The quality of worrying.
6 buffer into the vehicle line is too short
Buffer into the car line only designed 7 parking spaces, combined with the entire kiln car line design too little room for maneuver, once the blank system equipment can not be produced due to failure, a little longer, it affects the entire kiln car running. Empty kiln car unloading brick area, because the blank into the car line without empty spaces, empty place to place, will affect the burning brick can not be placed in time to unload brick online. In order to drive out on time, had to buffer into the car line of empty kiln roof over the code blank area, to unload the brick area of ??empty kiln car Teng location, so that often the empty kiln car drying kiln, affecting the drying quality .
7 No heat exchange ventilation system
Roasting, such as positive pressure operation, due to the poor roof sealing, there is flue gas outside the kiln, and the plant design, but also not in the kiln roof and floor cavity design heat transfer system, sulfur gas outside Leakage serious, on the kiln roof structure, steel plant erosion is very serious, coupled with the kiln roasting with the top of the workshop roof also did not design the exhaust system, but no design file smoke plate, the production workshop more than a year ceiling, vertical and roasting Of the 35m wide, 60m long color steel ceiling, has been rusty gas corrosion rusty, looking very Jiaoren heartache.
8 cast coal hole location unreasonable
The role of cast coal hole can not be overlooked, view the fire to adjust the fire, heating and cooling are all related to the kiln to the investment hole design in the middle of brick gap, the drawbacks:
First, the furnace once the temperature is low need to invest in coal, coal fell directly to the bottom, simply sprinkle (hanging) less than brick (should be projected down, brick stack edge should be displayed in the fire eye one-third) Oxygen contact surface is relatively reduced, heat is difficult to get full play, so that coal is not only low utilization rate in the furnace and the combustion speed and temperature is also slow.
The second is due to the investment hole design in the middle of the brick gap, from the concept of fire hole is difficult to see the two sections of the upper and lower billet temperature conditions, to bring some impact on roasting quality.
In addition, the total control room location is not appropriate, roasting workers to go to the top of the kiln, the need to go through the group, the host - Billet into the car line - drying chamber outlet - baking kiln into the car mouth - back to the firing kiln Central on the kiln top, back and forth need to take more than 300 m, very convenient. Aging of the library into the wind around, in fact, only play the role of transit library. Dry kiln with the top side of the air supply style, the design of 11 opposite the air duct, we in practice only open the three opposite side gate valve is enough to use (the rest have become ornaments), the actual drying effect is very good, brick crack , The average moisture content of less than 2% .Fume exhaust pipe is not set to clear the mouth, once there is dust or collapse of the brick plug ha outlet, do not cut the pipe or ceasefire can not clean. Kiln track below the road, which is a great risk, once the consequences of water would be disastrous. Kiln car repair pit design in the kiln car running through the place, once the kiln problems in need of repair, will delay before and after the kiln car operation.
If the design can take into account these drip problems, it will not be a problem, or even reduce a substantial investment. Unfortunately, these simple problems are not taken into account, to produce a lot of trouble. On the current actual situation, some problems can be transformed, some can not or temporarily unable to transform, can also need to increase the transformation of a large investment. This increase will reduce a great loss to the enterprise, I am afraid that is far greater than the design costs, if you consider the impact of production quality and yield factors, the loss is even greater. And therefore advise some of the construction of new production lines or transformation of the production line of investors, we must choose a wealth of design experience, responsible, formal design units, to prevent Huyou, causing significant losses.
- From the “brick” magazine
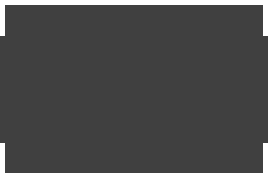
CONTACT
FOR ME
ONLINE SERVICE
400-027-6163
Manager Zhang 181-7117-9828
Manager Leng 138-8373-0415
Manager Zhang 181-7117-9829
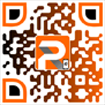
Phone
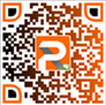
Wuhan Xiao Rui Machinery Co. Ltd.
Address: Wuhan City, Huangpi City Industrial Park, Ocean Park Tower Road No. 8
Telephone (fax):027-61636199
Chongqing Xiao Rui Machinery Kiln Equipment Co. Ltd.
Address: eight Chongqing town Dadukou District Mutual Industrial Park
Telephone (fax):023-68900571
COPYRGIT ? 2021 en.whxiaorui.com All Rights Reserved Powered by www.300.cn |